- Grover Tuning Machines
- Gotoh Tuning Machines
- Slotted Headstock Tuning Machines Ukulele Bass Guitar
- Slotted Headstock Ukulele
- Slotted Headstock Tuning Machines Ukulele Tuner
- Slotted Headstock Tuning Machines Ukulele Tuners
Peghed Tuners (or Peghead Tuners) are lightweight planetary geared tuners. They look like old style tapered friction tuners but have an internal 4:1 gear ratio and are lightweight which make them ideal for ukuleles. As a bonus they are made in the United States. Wow!
Named for the Kanile`a iconic two-pointed crown, this Tenor `ukulele combines the aesthetic beauty of Curly Hawaiian Koa, the clean look of Ebony and the practical function of a slotted headstock. Add to that the Kanile`a TRU-R (Total Resonating `Ukulele-Redesigned) bracing system with its touch-release-touch set up, geared tuners with an 18:1 ratio, a bridge pin system and Aquila Corde Super. Finally, we have guitar-style tuning pegs. This is the type of tuner that sticks out of the left and right sides of the ukulele’s headstock, on paddle headstocks, or face backward on slotted style headstocks. These are often the most accurate and easy to use tuners, with 14:1 gear ratio or higher. May 05, 2010 I opted for the Concert scale uke, and for something a little classier the slotted traditional headstock with backwards facing tuners. Was £179, though I think its a touch cheaper if you go for a standard headstock. On opening the box it was clear that this was a lovely instrument.
Peghed tuners are manufactured in right hand and left hand threaded pegs. The direction that the string tension pulls is the tightening direction of the threaded tuner.
The ‘normal’ right hand threaded pegs will be installed on the treble side and the left hand ‘reverse’ threaded pegs go into the bass side.
STEP BY STEP INSTRUCTIONS for #7543
Grover Tuning Machines
Step 1 - Drilling Holes
After laying out hole locations through drill the peg holes with approximately an .080” drill bit. Using a 1/4” Brad Point Bit drill halfway thru from the front side. Flip over and drill the other half way from the back side using the .080” pilot hole as a guide. This will prevent grain tear out from drilling in one operation.
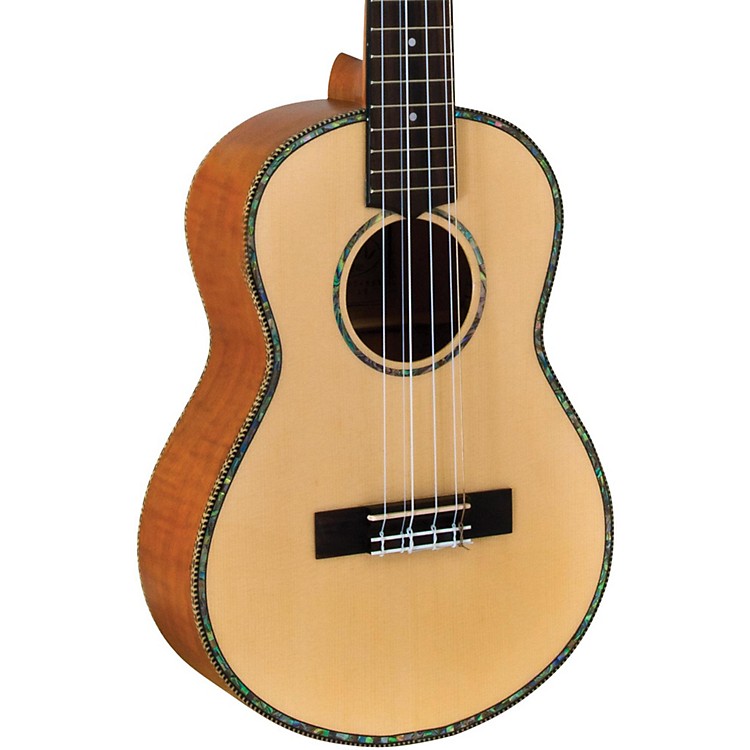
You will need a 30:1 tapered violin reamer, this is a different taper from a guitar peg reamer. Knock the handle off so it can be jigged in a drill press. Run at slow speed (approx 300 RPM) and keep the flutes brushed out to keep the tool healthy.
Determine the depth to ream the peg head to. Its a very good idea to use a piece of scrap wood similar in wood and dimensions to your peg head to practice with. The biggest mistake installing these pegs is over-reaming and making the hole too big, it’s not easy to make the big hole smaller.
The hole wants to be reamed approximately .030” smaller than the pegs diameter. Measure the smallest thread on the peg, subtract .030”, mark the reamer and ream to depth on your test piece.
Step 4 - Tools
Use rib-joint pliers with a thick leather pad to wind the pegs in.
Step 3 - Identify Left and Right Threaded Tuners
The pegs are right and left hand threaded. The right hand threaded pegs install into the treble side of the peg head and the left hand (or reverse) threaded pegs install into the bass side of the peg head.
The pegs should be just shy of showing their threads on the face of the peg head. Go slowly do not over ream. When winding in the pegs they will want to wander and go in anything but straight.
Watch carefully how they are progressing into the hole and do what it takes to coax them into going in straight. The nose of the tuner wants to come up and out of the middle of the hole on the face side. Watch the installation film to better understand the process. These pegs aren’t easy to install correctly but they sure are fine pegs.
Step 6 - Notes
Pay no attention to how the pegs turn in your hand before installation. You may not be able to turn them at all until they are installed.
Once installed the turning tension can be adjusted by pushing the button down to tighten up the turning tension or by pulling the button up to make them turn easier.
From the Spring 2017 issue of Ukulele | BY AARON KEIM
The tuning pegs on your ukulele are a vital piece of equipment. Whether you have a collectible vintage ukulele or a new, factory-made instrument, it’s important to get your strings in-tune quickly and reliably. When your instrument’s tuning pegs won’t cut it, they may need to be replaced or upgraded. But before we get into specifics, first we need to understand a few concepts of how tuning pegs are designed and used. Then we will discuss the different styles and their pros and cons.
The Tune, the Tuning
The first concept is tuning ratio. When you turn the tuner button, the shaft also turns. Old-style friction pegs have a 1:1 ratio, meaning that every turn of the peg turns the shaft one turn. This low tuning-ratio means that your movements must be smaller and it will be harder to fine-tune a string. Modern tuning pegs may have gears that can give them a tuning ratio as high as 14:1, meaning that every turn of the peg makes a much smaller turn of the shaft. (In this case, it takes 14 turns of the tuner button to make the shaft turn once.) As the number goes up, accuracy and ease of use increases.
The second concept to understand is weight. The ukulele is a relatively small and lightweight instrument. The more gears and metal parts your tuning pegs have, the heavier they will be. If you’re not careful, your ukulele will be out of balance and hard to hold, even with a strap. Only in the last few years have manufacturers been willing to design geared tuning pegs for the ukulele market that offer gears at lower weights and smaller sizes.
Gotoh Tuning Machines
The Simple Machines
The first type of tuning pegs to discuss are friction tuners. These can range from old wooden violin tuners to expensive modern replicas of golden-era designs. Friction tuners are traditionally used on ukuleles because of their lightweight and simple design. The most important thing to understand about these is that they have a 1:1 ratio. This can be problematic for fine adjustment, but if they are well made and installed properly, they can work very well. On the other hand, poorly made friction tuners can make your life miserable! Metal friction tuners usually have a small screw in the button that tightens the assembly, adjusting how easy or hard it is to turn. Too tight and you can’t turn the peg; too loose and the peg slips, making steady tuning very difficult.
If you have a vintage uke that needs old-style friction tuners with small shafts, I like the Waverly and Grover Champion friction pegs available from Stewart-Macdonald. It takes some practice to use friction pegs accurately, and some folks just don’t have the patience. If you’re one of those people, it may be a good idea to replace them with geared pegs.
Slotted Headstock Tuning Machines Ukulele Bass Guitar
The first type of geared peg I’ll mention are planetary tuning pegs, which get their name from the tuner’s internal gears, which resemble planets orbiting a sun. Like friction pegs, these tuners stick straight back from the back of the headstock. They are traditionally used on banjos and normally have a 4:1 ratio, which makes them easier to use and more accurate than friction pegs.
Slotted Headstock Ukulele
Advertisement
Until recently, it was hard to find planetary pegs that were light enough for ukulele, but now there are two good options. Peghed brand tuning pegs look like traditional wooden violin friction pegs, but actually have a 4:1 gear in the metal shaft. Their tension can be adjusted by lightly pushing in or pulling out the button until the tension is just right. They are very lightweight, but require a tapered hole in the headstock, which means you may want professional installation. The new Gotoh UPT planetary pegs are miniature versions of the company’s popular banjo pegs and are another great option. They don’t require a tapered shaft and come with multiple finish and button options to match the aesthetics of your instrument. They are a little heavier than Pegheds, but still appropriate for most ukes, especially tenor and baritones.
Finally, we have guitar-style tuning pegs. This is the type of tuner that sticks out of the left and right sides of the ukulele’s headstock, on paddle headstocks, or face backward on slotted style headstocks. These are often the most accurate and easy to use tuners, with 14:1 gear ratio or higher. In the past, guitar-style tuners were too heavy for ukuleles, but now there are many lightweight versions. My favorite is the old-school Grover open-back tuners, scaled down from the classic guitar design with shorter shafts for ukulele. If you want an even fancier version of this style of tuner, check out the beautiful wooden knobs on the Waverley.
Grover’s Sta-Tite geared tuners.
No matter what you choose for upgrade or replacement, keep in mind that every tuner requires a different size hole in the headstock. Don’t assume that your new pegs will drop right in. If you’re experienced with tools and woodworking, this isn’t a problem. But, if you’re worried about it at all, ask your favorite acoustic music repair shop to handle it.
Slotted Headstock Tuning Machines Ukulele Tuner
No matter which quality tuning pegs you choose, it’s worth the cost to keep your ukulele playing in tune!
Slotted Headstock Tuning Machines Ukulele Tuners
Aaron Keim is a luthier at Beansprout Musical Instruments (thebeansprout.com) and also a busy educator, historian, writer, and performer. He performs with his wife Nicole in the Quiet American, an old-time folk music duo based in Hood River, Oregon. quietamericanmusic.com